TEAM- “Together Everyone Achieves More”
That cliché never gets old, especially when dragging heavy rolls of turf all day long. I have always experienced accomplishing larger goals in life while being part of a TEAM. Wikipedia states that “Teamwork is the collaborative effort of a group to achieve a common goal or to complete a task in the most effective and efficient way”.
Creating a good “turf team” is crucial. I teach companies teams how to be a team. Just because you have a few guys with knives does not make them a team. A “turf team” requires installers that care and have passion for their actions. To be good at something in life you must care for what it is. If you create a “turf team” and have a member that does not enjoy cutting synthetic turf, I would give them tasks outside the “turf team” or have them go to work for the competition and drag them down. Great turf teams have members/installers that bring forth synergy to show their talents and blend strengths. When establishing a turf team, it is important to break down each task for each member. This may mean creating tasks for each member on every installation. I recommend dedicating tasks that match up with skill and experience.
This month ASK JW will explain how crucial teamwork is to being a successful turf contractor/Installer.
“If you are looking to install synthetic turf solo, without any help, or assistance, this column is not for you. If you would like to build a successful Installation team in the synthetic turf industry, keep reading”.
JW
I often ask company owners what their team’s vision is. They look at me like I am speaking another language. I feel every turf team should have a team vision. Team vision is when all members of the team share a common goal and understand each task that needs to be accomplished to have successful repetitive turf installations. Each member must play a role in the vision together. I recommend sitting down with your team and discuss their vision for their position and how they can contribute. This will show how serious you are about wanting success in the synthetic turf biz’. If you have not created a team yet, this column will give insight into what may be needed for your team to thrive.
“The Interview”
“You are only as good as your frontline”
JW
Qualifications
When establishing a turf team, it is crucial to know how much experience each team member has at installing turf. Other than filling out the company’s job application, it is important when building a team to know each other’s capabilities, strengths, and weaknesses.
Below are a few basic questions that I recommend asking installers prior to having anyone cut into a section of turf.
- How many years of experience do you have?
- How many synthetic turf installations have you completed within the last year?
- What are the “beginning to end” steps for installing turf?
- Do you own your own turf tools?
- What is a loop/pile push cutter?
- What is a gauge in synthetic turf?
- What is a stitch row?
- What is pile height?
- What is dye lot?
- How do you prevent wrinkles when installing synthetic turf?
- How do you seam two sections of synthetic turf together? Explain in detail.
- How much experience do you have making repairs to turf?
There are many other questions pertaining to synthetic turf that you may ask the installer prior to stepping foot on the project. Experience is very important for a successful turf team. If your installers are beginners, your installation will exemplify this.
Ask for references and projects that they have been a part of. If you want to have the best team, then you will need the best team members.
Team Size
I recommend creating an adequate team size. A successful turf team must include at least 4 or more members. Teams may change in size depending upon the size and complexity of the project, especially if the installation requires placement of very large long sections.
Teams need clearly defined roles within the team in order to create beautiful installations. Efficient teamwork is created when each member takes on the responsibility for each task they perform. When each task is repeatedly perfected, it produces success which makes each member feel accomplished and inspired.
Chemistry
Having good chemistry is like “working gears”. If a gear is out of sync, then the teeth of the gears will not fit together and cause issues, sometimes destruction. When creating installation teams, chemistry between team members is crucial. Personality types must be cohesive, otherwise, performance may become less efficient. If team members exemplify poor communication within the team, conflicts may arise and slow down progress, and/or quality of the installation. There must be continuous lines of communication to avoid all conflicts to keep the gears spinning smoothly.
Sales members and office personnel are just as part of the team as the installation team itself. Having chemistry between the frontline and the office is the key to fluidity. Teamwork starts with the sale, communication with the office, then to the frontline.
Coordination
co·or·di·na·tion
- the organization of the different elements of a complex body or activity to enable them to work together effectively. – cooperative effort resulting in an effective relationship.
Perfecting tasks is one thing, but having poor coordination will slow down production and may produce conflict between team members. Each installation must be coordinated to ensure success. This means prior to arrival on-site; material ordering, shipping, manpower, client communication, location, and complete installation including clean-up. Without coordination, a team will have confusion.
Co-Operation
co·op·er·a·tion
- noun-the process of working together to the same end.
I am sure everyone has heard the saying, “there is no I in team”. Well, there’s not”.
And there is no “I” in a synthetic turf team as well. If you choose to do a solo career, then the turf biz is not for you. Cooperation is needed to perform the steps it will take to produce the results.
“Without teamwork, you may only become a “side-jobber”.
JW
Leadership Positions
Sharing responsibility heightens teamwork. Equally sharing leadership positions builds team confidence and allows for multiple installations to go on at once. This will give team members the feeling of responsibility and makes each member accountable for their actions. I recommend having a team leader for every crew. This will bring accountability to one person’s qualification delegating tasks for each member. The team leader must have experience at all levels of installing synthetic turf. He/She must understand each project’s complexity and the ability to complete it with high standards.
Teamwork & Plan B
Planning is a big part of teamwork. If you have no plan, then eventually your team will fail. Even for the ones who plan well, things don’t always go according to plan. Often, we may come against obstacles that we did not plan for. As leaders we must remain calm and not react. “What can go wrong will go wrong”.
To be successful in the synthetic turf industry one must have experienced all that can go wrong. When you have a great leader that understands the “what ifs”, then he/she can make sudden decisions for the team and rapidly create a “Plan B”. Decisions like having a member damage an irrigation line and you have a flood on your hands destroying the entire graded area. A good leader knows how to react in sudden circumstances to alleviate the stress upon the team and the company’s reputation.
Teamwork Performance Evaluation
When establishing a synthetic turf team, I recommend creating a “Teamwork Performance Evaluation”. This evaluation will recognize the team’s strengths and weaknesses. This will allow the team leader to evaluate each installer’s performance for the task they are given. If a team leader sees that another member is lacking on a certain task, it is up to that team leader to get them up to speed or place that member on a different task. Having a successful synthetic turf team means all members working together. If your team is out of sync you may have to have a team meeting and get them back working in unison.
I recommend taking the time to ensure your team is up to date with the latest technology, tools, and machinery that are available in the industry today. Take time to train and retrain team members between seasons. Never allow teams to become stagnant in craftsmanship. There are so many exciting changes in the synthetic turf industry today that allow turf installers to hone their craft, plus you can always rely on “ASK JW” for all the latest tips, tricks, and educational information.
Safety & Teamwork
Synthetic turf may look like an easy profession, but it has its share of mishaps. You would be amazed by the injuries and accidents I have witnessed over the years due to the lack of understanding of safety in this profession. When your team or teams are established, it is important to create team safety meetings.
Team safety meetings are not only crucial to the company but in many states required by O.S.H.A.
Team safety meetings provide an opportunity for management to communicate to employees how they can do their jobs safer. Safety meetings allows employees an opportunity to speak about safety and health concerns or workplace improvement ideas to their co-workers, supervisors, and upper management. Unsafe acts account for 90 percent of all accidents. Safety meetings teach preventative measures against unsafe acts by educating employees on how they can do their job safely. I recommend creating a safety manual that will discuss safety concerns for each component that goes into your installations. For example, Dealing with sharp blades – Hand protection, Blade Container.
Team Safety Meetings allow employees to have a better understanding of turf safety prior to starting any project. Safety meetings can happen during the project as well. When a supervisor witnesses a violation of safety, it is advantageous to have a safety meeting to address the issue at hand immediately. “No pun intended”.
Teamwork & Delegation
There is a process, sequence, and order when installing synthetic turf. You cannot start to place infill if seams are not glued, edges cut in, and the turf completely secured. When a team is created, the team leader delegates tasks in sequence from start to finish. This includes who will be on a shovel, wheelbarrow, or rake. This includes who will be cutting edges, and who will be following securing the edge.
Merriam Webster defines “task” as an assigned piece of work that is needed to be completed within a certain time.
Like I mentioned at the beginning of this column, this column is all about teamwork. You may accomplish these tasks/steps by yourself for smaller projects, but working solo won’t get you anything but a few hundred square feet a day. Teamwork can get you 10,000+ square feet a day with minimal team members.
It is all about creating a power team that can respect and accomplish their tasks productively in a timely manner. Many larger projects have deadlines to meet. Having a solo mentality will not meet them.
Below are several tasks/steps where teamwork prevails when accomplishing larger projects.
Nailer Boards
I recommend a 2 to 3 member team when placing plastic composite nailer boards. Many larger installations specify 20’ long nailer boards. Securing these long sections at a certain elevation can be tricky and strenuous.
REMEMBER: The nailer board team must stay ahead of the grading team.
Grading
Depending on the size of the project and how much equipment you own, grading may require many team members. You may need extra labor just to transport the materials to the location, or less if you have a bucket loader. The image above was a picture I had taken at the Williams Field High School in Gilbert Arizona. I was hired to consult, strategize, and put together production teams in making a crucial deadline installing 41,000 sq. ft. in 11 days. The high school was opening within weeks. This meant red-head 6,400 lineal feet of nailer boards, grading, and compaction of 1,400 tons of materials (tested at 95%), installing and seaming 41000 sq. ft. of synthetic turf with 2 pounds of infill. If teamwork was not in the mindset of everyone on this project, the deadline wouldn’t have been met and the general contractor and the landscape company would have been in default and incurred costly penalties.
Weed Barrier
If you are an experienced turf installer you definitely had your share of wind & weed barrier. Weed barrier materials can be easy to roll out and place but can be more productive with two or more installers. Keeping it tight is rule #1. Going solo in placing weed barrier not only takes more time but can get out of control if the wind starts to kick up.
Transport
Transporting and handling of synthetic turf can be the most draining, labor-intensive thing on this planet… or it can be the easiest depending on how many team members are assisting. A full roll of turf can weigh up to 1800 pounds. Transporting and rolling out several rolls a day can be exhausting. I recommend getting everyone including grandma, grandpa, and the neighbors to help when transporting and rolling out synthetic turf – I am just kidding. If you must transport a full roll without machinery, I recommend getting every team member to assist. You will never ever have enough help when transporting heavy rolls of turf to and fro’. And remember to wear your back belts!
Securing
Securing turf is crucial. There is more to securing than placing a few nails/spike to keep in place. The sections may need to be stretched prior to securing which may take more than one person to accomplish.
Seam Perfection
“If you are installing seams, make sure you have enough manpower per foot. If you short cut on labor, your seams will come up short on quality”
JW
Any group of installers can become experts at seaming if they create a team, tasks, and act of execution. You must have plenty of help for the length of the seam. This allows controllability. The pictures above show plenty of Team Members assisting each other in “Seam Perfection”. As you can see, they have full control of the two sections.
Seaming Tape & Adhesive
I recommend having as many team members involved when it comes to placing seaming tape and adhesive for landscape turf.
- Two or three members can place seaming tape efficiently and stay ahead of the adhesive placement. All joints must be opened, seaming tape must be secured to the center and kept flat.
- Depending on the size of the project and the number of seams, I recommend having a minimum of 3 team members placing the adhesive. One member dropping the adhesive from the container. The second member primer/spreading the adhesive with the correct notched trowel. The third member following second member knocking down high spots and completing the required depth.
Seam Connection
When securing seams with adhesive, it is extremely crucial to have all team members assisting on the final connection. It is also important to have a good leader at the front delegating movement and personally connecting the two sections together. Depending on the length of the seam, I recommend having each member approximately 6’-8’ apart assisting in lowering both sections for the “Seam Leader”. Having enough members and evenly spaced prevents the fibers from touching the adhesive. Members can drop off the line the further you get to the end of the seam.
Seam Compression
Most objects or materials that are to be unified by adhesives need some type of compression while in its curing stage. Compression allows the adhesive to be forced into voids and capillaries within its adhesive zone and ensures the bonding performance. Do not chance seam failure, keep compression on your seams until the adhesives are cured. When using Superseam Adhesives, I recommend having enough members assisting in the placement of 50lb infill bags for compression. The sooner the compression, the faster the “Curing Stage”.
Infill Placement
Determined by the square footage, and number of pounds to be filled, I recommend having enough labor to place and brush infill into the surface without wearing your team down. Infill placement if like fourth quarter in a football game. We are almost done, and we need the entire team to pitch in and finish up what is at hand.
This may mean one member on the drop spreader, one/two members transporting the infill bags, two/three members brooming it in.
You may go online at www.turfbrush.com and get yourself a turf brush attachment and save on labor. It places and brushes the infill in the fibers at the same time!
Defibrillation
Defibrillation (Powerbrooming) is one task that is not a team effort, but is it? I do know that a talented and knowledgeable team member on a power broom can complete an installation and make it come alive! If your installation is massive then you may want to consider using one, two, or three members on power broom machines. If this is the case, then the team of defibrillators will need to have a game plan and direction. This will need to be coordinated to ensure a beautiful finished product.
Putting Greens
Successful putting green installations requires a talented team. The responsibility is heavy for team members creating a putting green surface that will suffice a professional golfer. A lot goes into a successful putting green and it takes teamwork to pull one off. From creating radius points, concreting cups, securing the fringe, seam tape, and adhesive. This all takes talented teamwork.
Sand/ Grass Traps
Installing Sand and Grass Traps will never be a one-person task. Not if you want them to look like the center image above.
AirDrain Traps
Installing AirDrain grids productively requires a set of Teamwork. A team must be formed and a game plan must be made to productively place AirDrain Grid in large areas. I recommend one member handing the AirDrain grid to the front member. (image to the left in blue shirt) and third member assists in the locking of the tabs.
Shock Pads
The #1 issue in the shock pad failures today is the care of the placement. Shock pad edges are cut straight, clean, and sent from the manufacture in good condition. When placing a shock pad without enough team members, one must fight to have to keep the edges from getting damaged and loose. When the edges are damaged or loose, this will bring the quality of the installation down. The shock pad may reach its H.I.C. numbers for the drop, but the edges may “mirror through” the top surface. Dragging them will damage them. Make sure you have a plan of action and enough team members to successfully place shock pad.
Repairs
Repairs always turn out flawless when you attack them as a team.
Maintaining synthetic turf can be a really hard task. You should see how much particles and vegetation scraps get pulled out of turf when maintaining it correctly. Depending on the size and how good you want the turf cleaned, this can be a very hard “One-Person-Job”. I recommend not doing it alone. Depending on the size of power brooms, and the size of the area, you may need multiple team members to accomplish the maintenance correctly and in one day.
“Be part of a team or lead one”.
JW
For more information regarding creating a successful synthetic turf team, or to schedule a training please contact J.W at 888.846.3598 or email AskJW@SGWcorp.com
Suggestions for the use of ASK JW installation techniques are solely at the end-users’ discretion; however, the user should determine suitability for the intended use by his/her own evaluation. Because the use of the materials is beyond our control, neither ASK JW nor SGW shall be liable for the outcome of any use of said materials including any injury, loss, or damage, direct or consequential, arising out of the use or inability to use these techniques and products.
Other Topics:
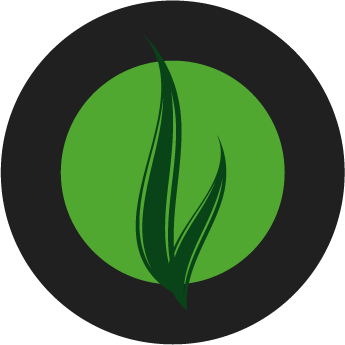
About SGW
Learn more about SGW
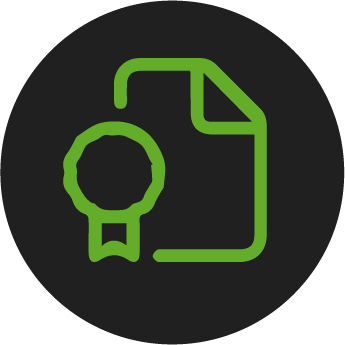
Certifications
IPEMA, Lead-Free, and CAD Details
Warranties
Our Industry Leading Warranties
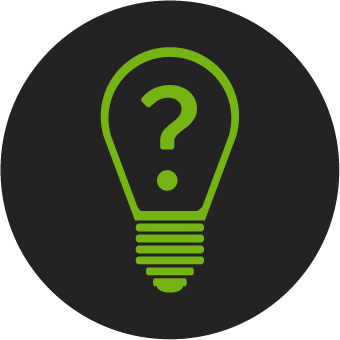
Ask an expert
See if we’ve answered your questions
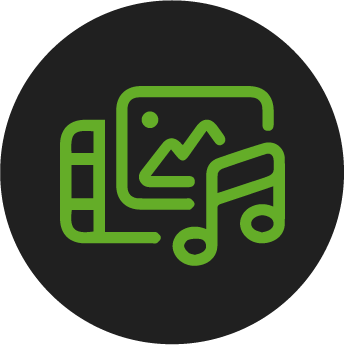
Media
Our tried and true steps for installation
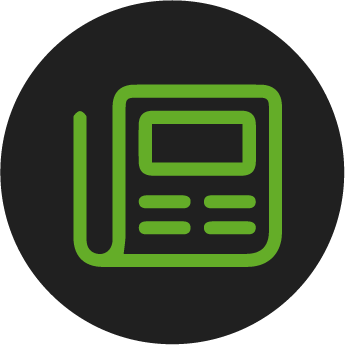
Blog
Learn about our turf in depth
Here to help
Our Commitment
We are committed to providing the best artificial turf products at competitive prices. Our warehouse carries the most advanced synthetic grass products available, engineered to look and feel like real grass. Every turf product is made with high quality materials that are safe for everyone, especially children and pets.
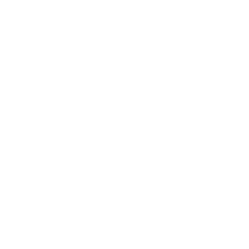
Industry Leaders
SGW Canada has always stood out among competitors, offering new products with the latest technology.
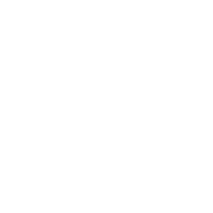
Service Oriented
The only thing better than our grass is our customer service. Our staff is committed to providing the best experience possible for our clients.
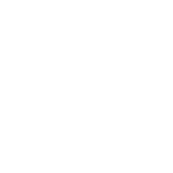
Quality Driven
At SGW Canada we only offer products that maintains a high standard of quality. Backed by up to a 15 year warranty, the best in the industry.